Summary
For more than a century, Salt River Project (SRP) has produced power and delivered water to meet the needs of its customers in the greater Phoenix metropolitan area. Today, as one of the nation’s largest public power utilities, SRP provides reliable electricity and
water to more than 1 million customers and employs around 4,500 people. In order to produce power, including generation, transmission and distribution, to this 2,900 square mile service area, SRP uses a combination of hydro, gas turbine, coal fired, nuclear, solar, geothermal and wind generation. Furthermore, SRP is the largest water supplier in the Phoenix metropolitan area, responsible for water transmission and distribution for a 375 square mile service area while managing a 13,000 square mile watershed. This water production, transmission and distribution includes an extensive system of reservoirs, wells, canals and irrigation laterals.
30 min
Time saved per calibration using an automated approach
1000 hrs
Overall amount of man-hours saved after implementing the new solution
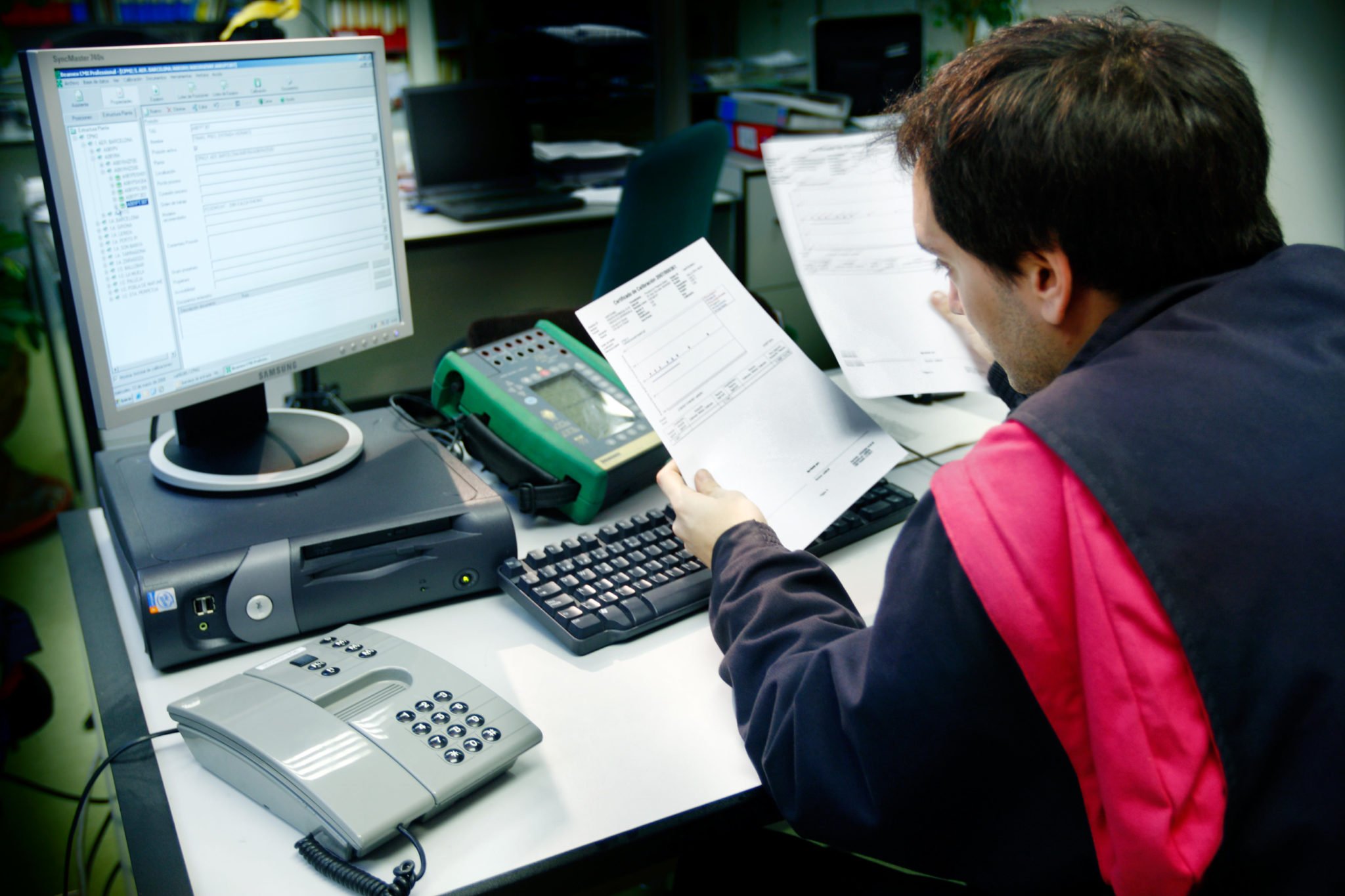
Small steps for a big evolution
In 2005, Jody Damron, a Business Analyst at SRP’s corporate headquarters in Tempe, Arizona was a member of the International Society of Automation (ISA) Executive Committee. While attending an ISA conference, Jody was introduced to Beamex CMX calibration management software during a technical “how to” presentation.
He recognized the importance of the increased functionality that calibration software offered over and beyond the current set up. At the site, his technicians reviewed it and also saw the value, they especially liked the user-friendliness along with the ability to capture more information than they could with Access.
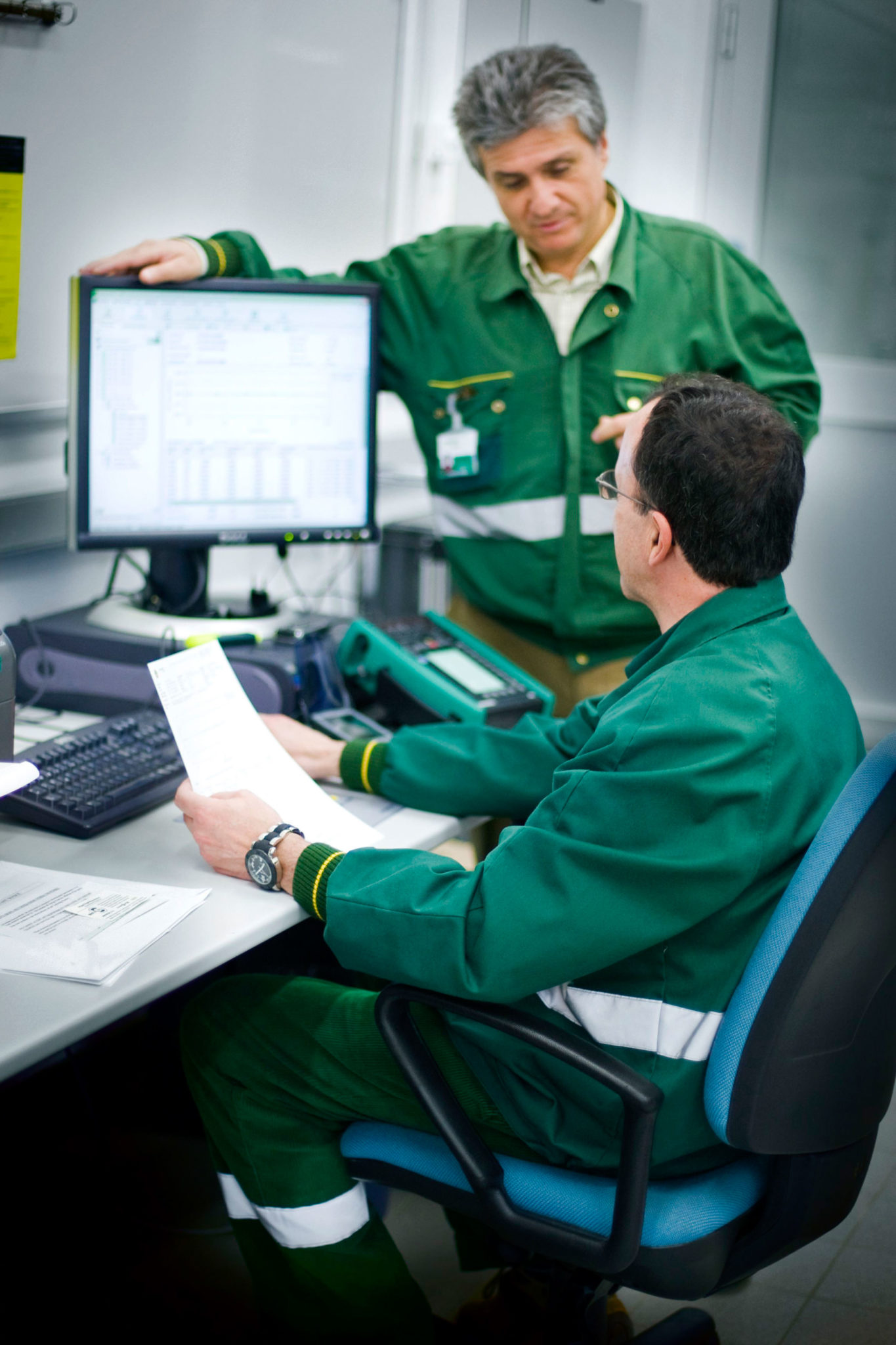
Continuing problems
Jody, IT and a Maximo contractor were tasked with replicating all of the Access application functions along with instrument and control data into the corporate work management system, Maximo. It was a difficult project, but the team was able to duplicate most of the functionality they used in Access.
Major accomplishments included more secure data, improved calibration reporting capabilities, less stressful state audit reports, links to drawings, documented DCS points, asset data comparison, a better governance process, and more detailed instrument meter data. However, there were still inefficiencies, costs were high and significant manual oversight was required.
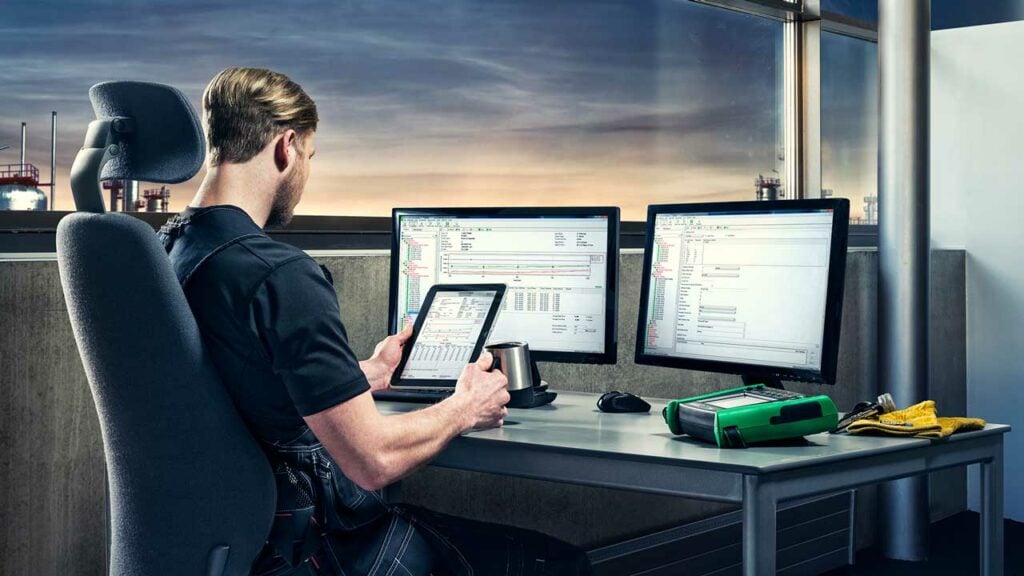
Need for a better solution
In 2012, Jody became the generation Business Unit Representative with the responsibilities of leading the generation team and interfacing with IT to implement Maximo and SAP. This project partnered the instrument shop’s valuable experience with the IT developers to meet business requirements.
Maximo was upgraded from version 5.2 to 7.5, which included a new “built-in” calibration module. The technicians tried using the Maximo calibration system, but they pushed for CMX to be integrated into Maximo because they needed a calibration software that offered more comprehensive features.
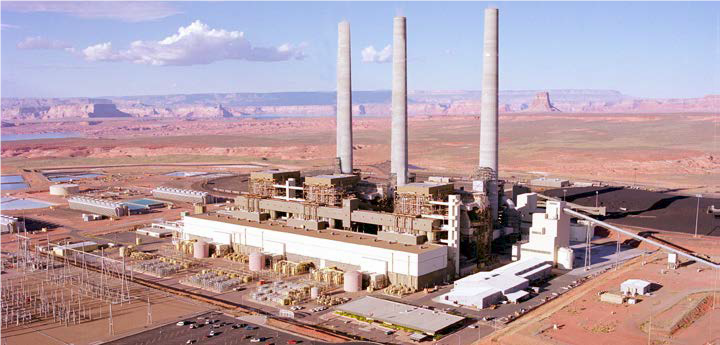
Read the full Salt River Project customer case story
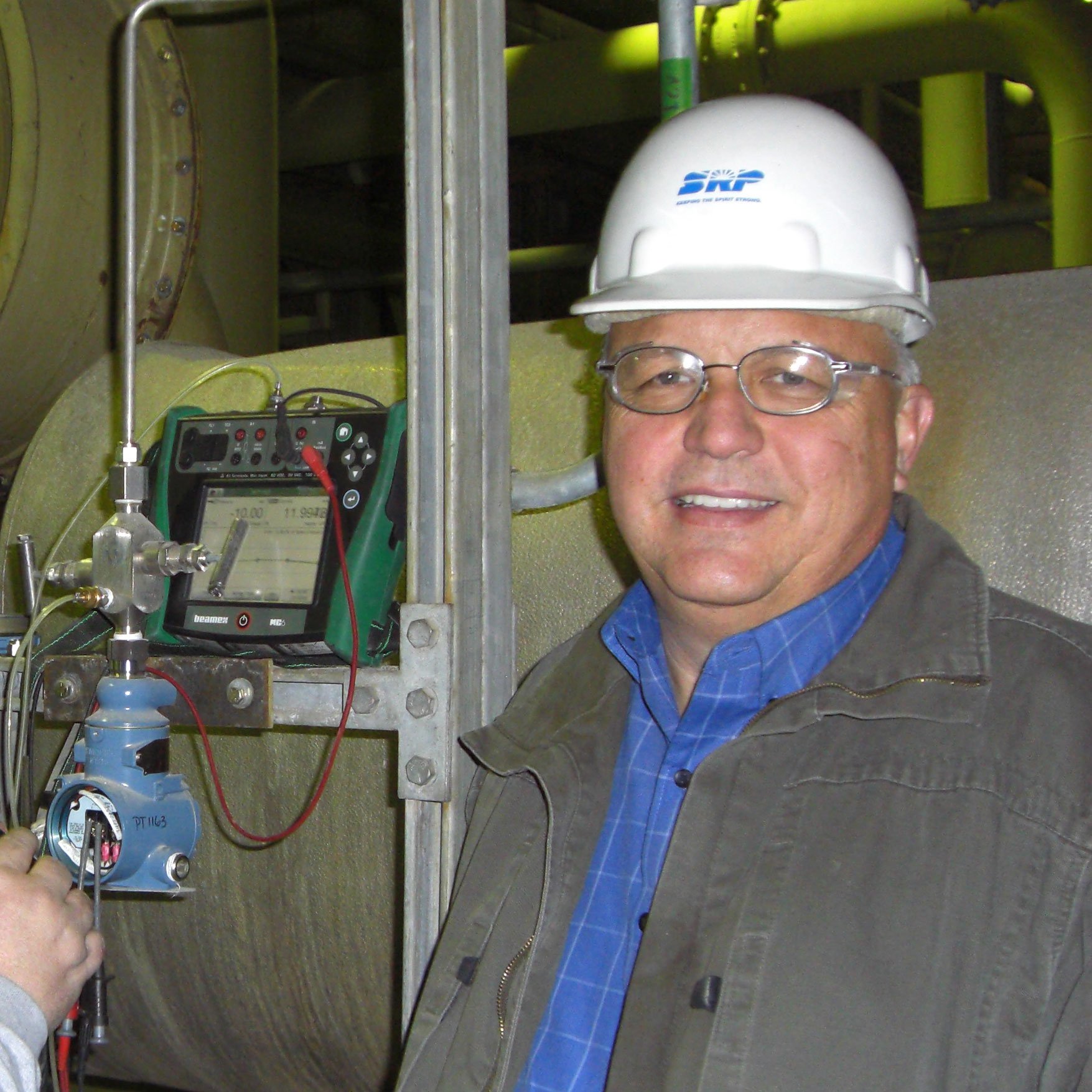
Summary & Results
Close attention to detail and building a trusted, quality project team both internally and from their vendors were crucial factors to SRP’s many successes. As a result, Jody explains, “With this software integration project, we were able to realize a significant return on investment during the first unit overhaul. It’s unusual, since ROI on software projects is usually nonexistent at first.”
The most significant impact overall is that Salt River Project has been able to save about 30 minutes per calibration using an automated approach. This equates up to 1,000 man-hours in the previously cited unit overhaul example. Further savings are anticipated as history analysis will confirm that extended calibration intervals are recommended. It is important to note that SRP’s work order history for calibration is 100% automated and technicians never work in Maximo.
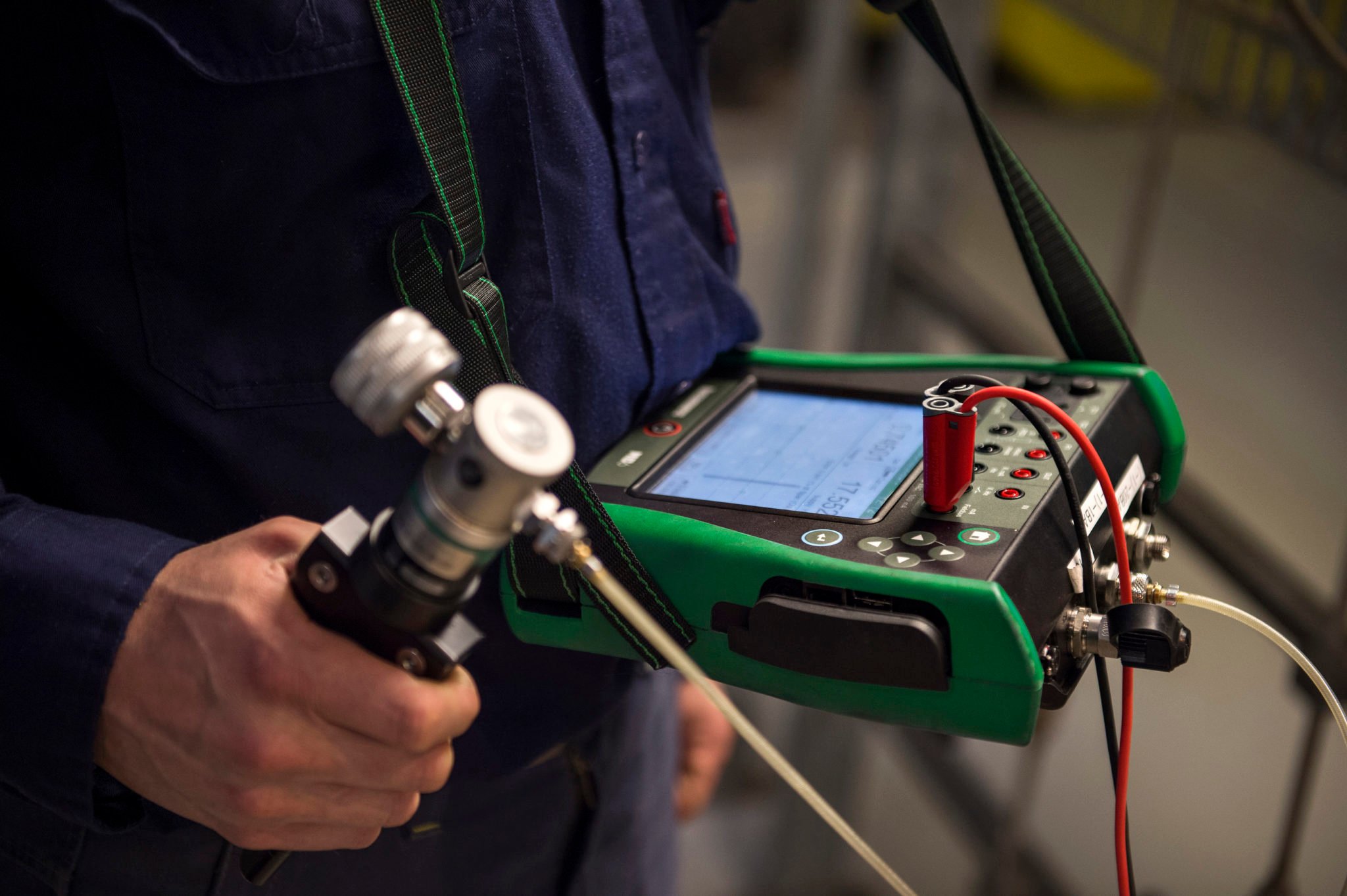
Project review
Throughout this process, Jody notes some key factors he recommends to keep in mind when implementing a calibration process change:
- Do not compromise data integrity.
- Build a solid team.
- Set realistic timelines.
- Set expectations and interpretation guidelines.
- Document the business process.
- Build a governance process.
- Support the new process.
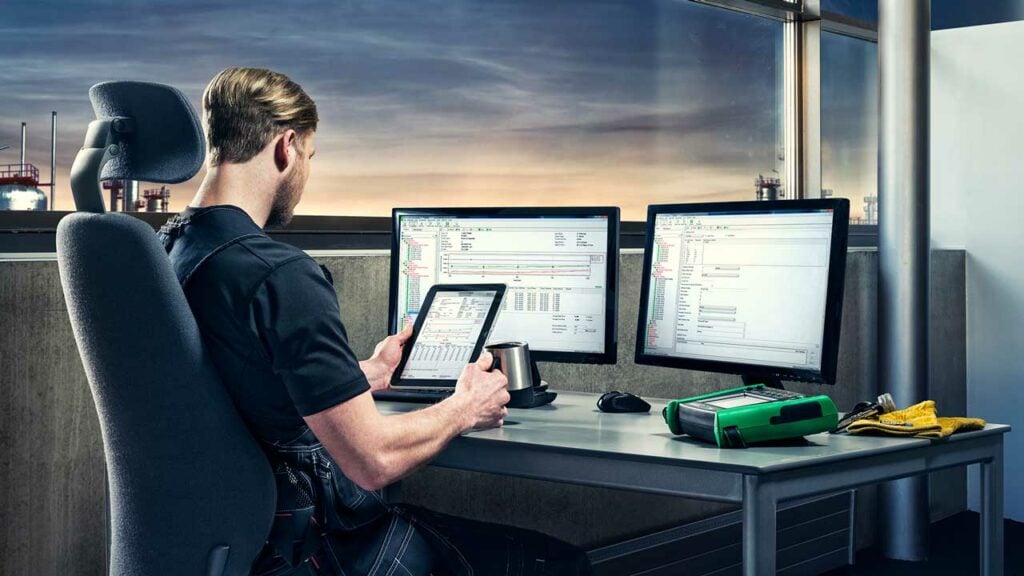
Major benefits of the automated calibration solution
- System oversight has been minimized.
- Audits are easy to perform and are less stressful.
- Defined calibration procedures provide a corporate “best practices” approach to calibration.
- Better decision making because of accurate data.
- In the simplest terms, the new Beamex/Maximo calibration system gives back time to the people working in the field.