Summary
As one of the UK’s leading full-service engineering providers, OCU Hornbill Ltd, has taken huge strides forward in the market thanks to its partnership with Beamex. The combination of advanced, multifunctional calibration hardware and user-friendly software has given OCU Hornbill a sharp competitive edge in the crowded UK marketplace, helping it win new contracts and provide faster, more efficient service for its highly diverse client base.
Market-leading service quality underpinned by Beamex solutions
OCU Hornbill operates two Beamex MC6 Advanced Field Calibrator and Communicators alongside multiple pressure modules and external transducers. As part of their work, technicians also use Beamex CMX calibration software to manage and maintain clients’ instrument databases. Beamex solutions are used daily to calibrate pressure, level, and flow transmitters as well as resistance temperature detectors, thermocouples, and pressure switches.
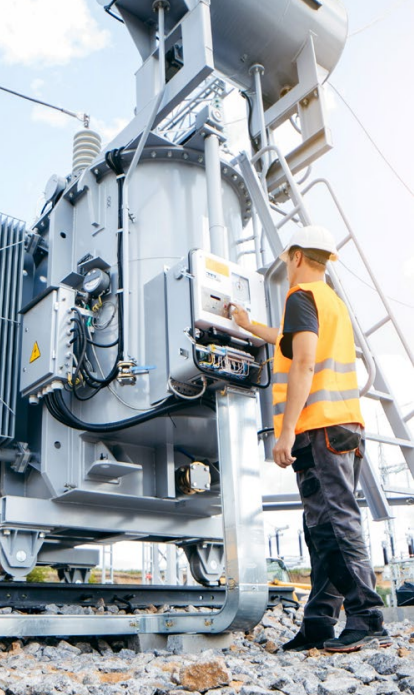
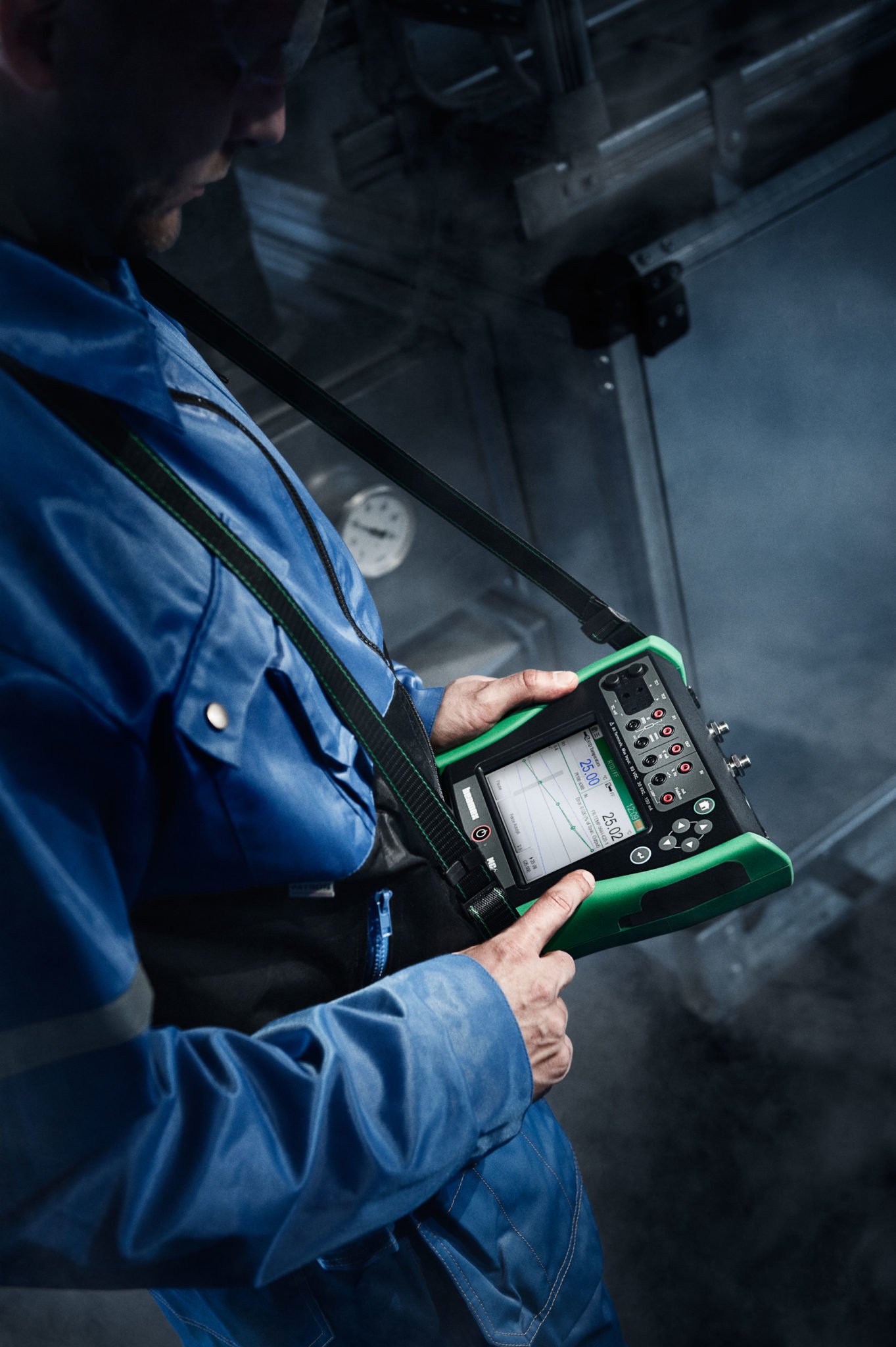
Building a lean, mean calibration machine
With Beamex calibrators and software now an integral part of their field operations, OCU Hornbill’s technicians are far better placed to execute their work efficiently and maintain the high level of service that their clients have come to expect over the years.
“Since moving to Beamex our processes are much quicker and more efficient,” Matthew says. “We can simply download the data to the calibrator so all the information we need is in one place. Beamex provides a fantastic platform for building an extensive calibration history so we and our clients can track trends and forecast when an instrument is likely to need replacing, for example. What’s more, the handover process is so much easier with the certificate option. We can now generate calibration certificates in seconds and share them with clients instead of handwriting them or typing them up after the job is complete.”
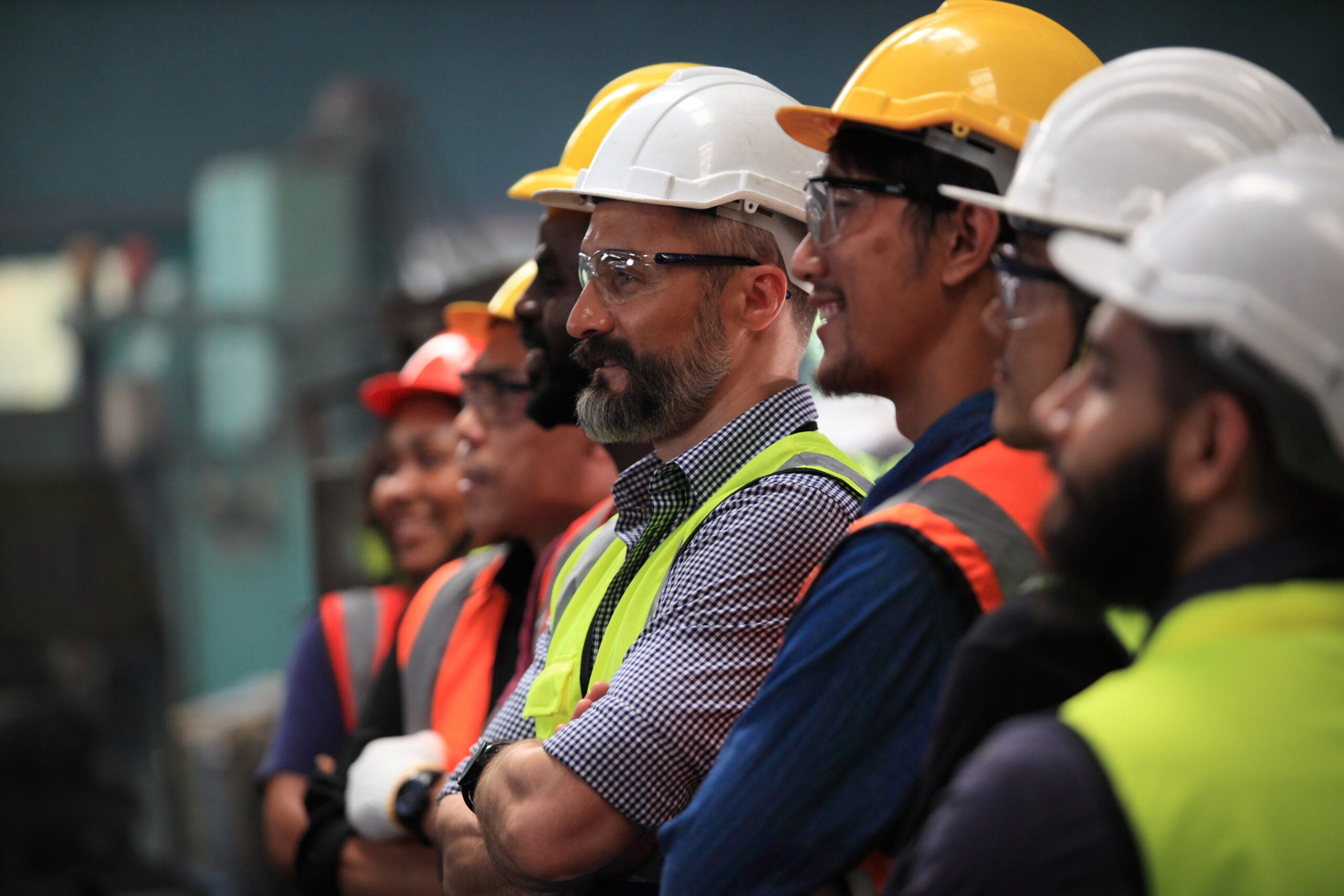
Read the full OCU Hornbill case story
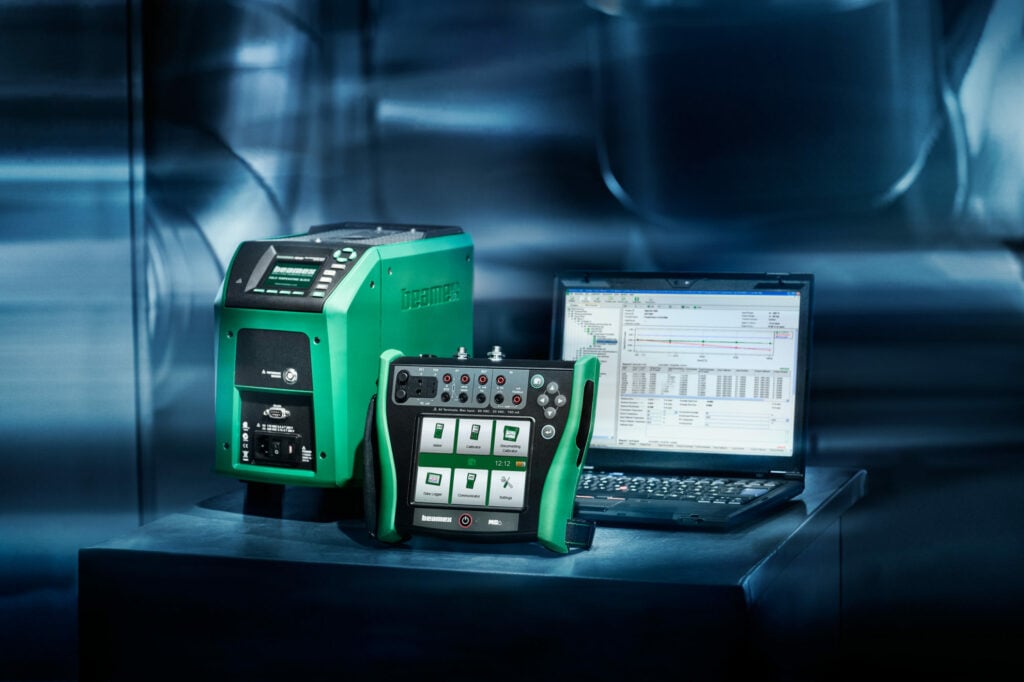
New opportunities on the horizon
Today, using Beamex solutions is even a qualifying criterion for some of the tendering processes that OCU Hornbill is involved in. “It’s safe to say that without Beamex we would be missing out on multiple potential new contracts,” Matthew points out.
“Put simply, Beamex makes us a more attractive prospect in the market, primarily because of the excellent traceability it brings but also because of the economic benefits too. With Beamex hardware and software we can deliver our services more efficiently while maintaining high standards of quality. We see the relationship with Beamex developing in a number of ways in the future. We plan to expand our use of Beamex products and software, and we are also interested in exploring the use of the bMobile application for ATEX inspections. There’s a lot to look forward to!”