Summary
Kevin works at a water and wastewater utility in the southeastern United States. The utility was founded in 1968 and today provides essential drinking water and wastewater treatment services to around 250,000 people. Following his promotion to Instrumentation Superintendent at the utility’s Electrical Systems Department, one of Kevin’s first tasks was to identify and implement a calibration
software database. “With a computerized database we would be able to do away with the time-consuming and error-prone system of recording calibration data with pen and paper before entering it into an Excel spreadsheet,” he explains.
Beamex checks all the boxes
Kevin’s first step was to contact the International Society of Automation for help obtaining a list of calibration database software companies. Trimming down the list of more than 25 potential candidates to a top three took some careful online research and multiple phone calls with sales representatives.
“After this process it was clear to me that Beamex was the top choice as our partner for calibration excellence because their offering best matched my checklist of requirements,” Kevin continues. “First and foremost, I wanted software that was scalable so it can grow with our needs. I also wanted to be able to reduce the number of field calibrators in use, minimize the human error factor, and reduce the time needed for calibrations. Being able to generate traceable calibration certificates was also a must.”
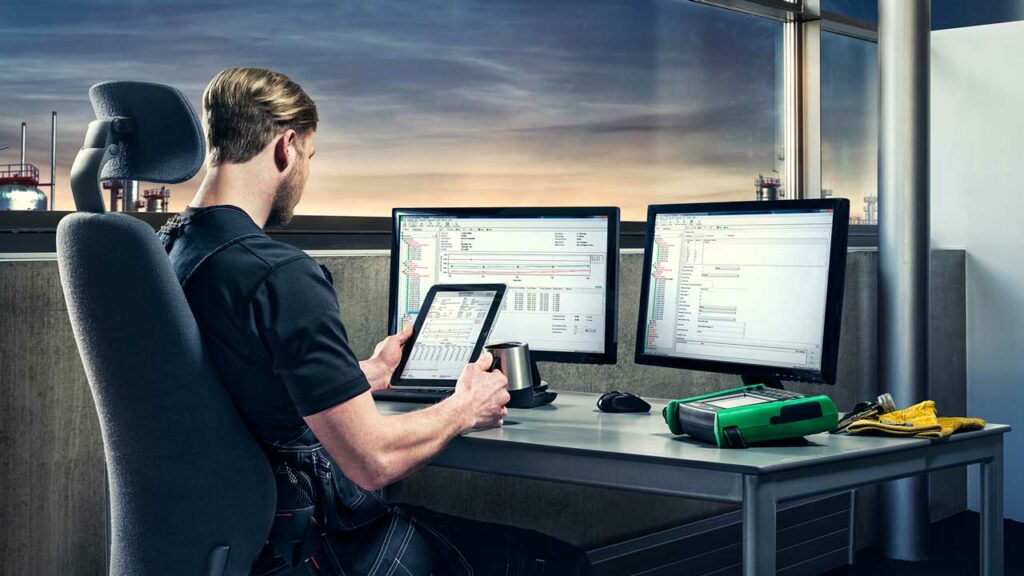
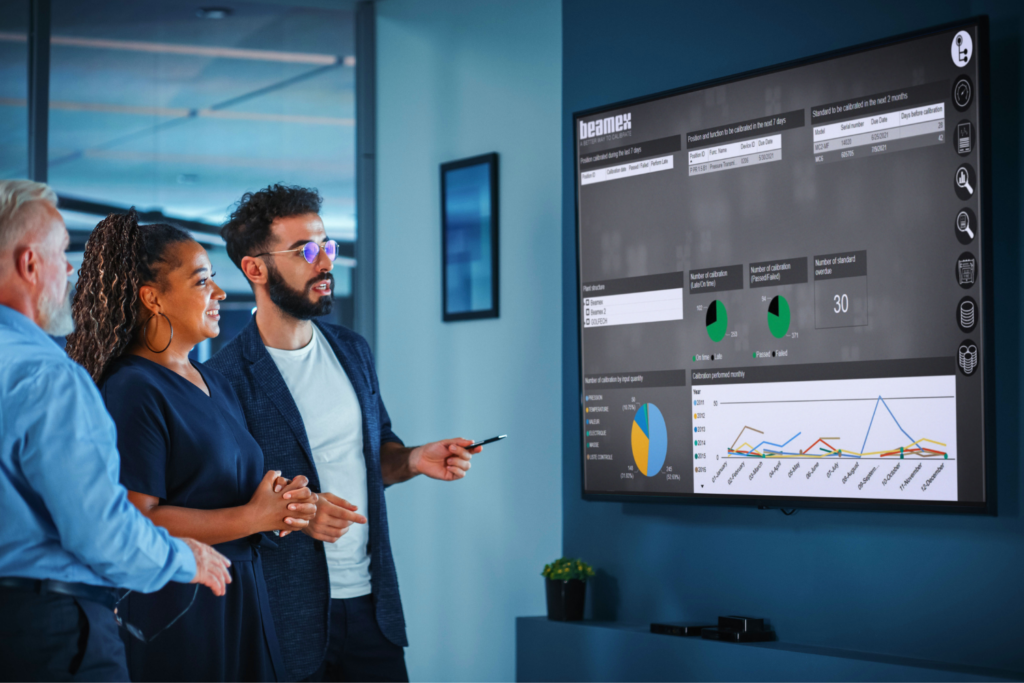
The journey to time-saving digital calibration management
Prior to joining the Beamex calibration ecosystem, the water and wastewater utility was using Microsoft Excel to manage the calibration data generated from its more than 1,200 instruments.
“The first step was to meet the Beamex sales rep to review our existing calibration management system. He recommended a Beamex CMX Calibration Management Software database with 5,000 instrument positions,” Kevin explains.
Alongside this, he recommended the Beamex MC6 Advanced Field Calibrator and Communicator because, in Kevin’s case, it would replace four existing field calibrators per technician that needed annual calibration. The MC6’s communicator mode is designed to
communicate with fieldbus instruments, allowing technicians
to calibrate, configure, and trim instruments without having to
carry additional equipment in the field.
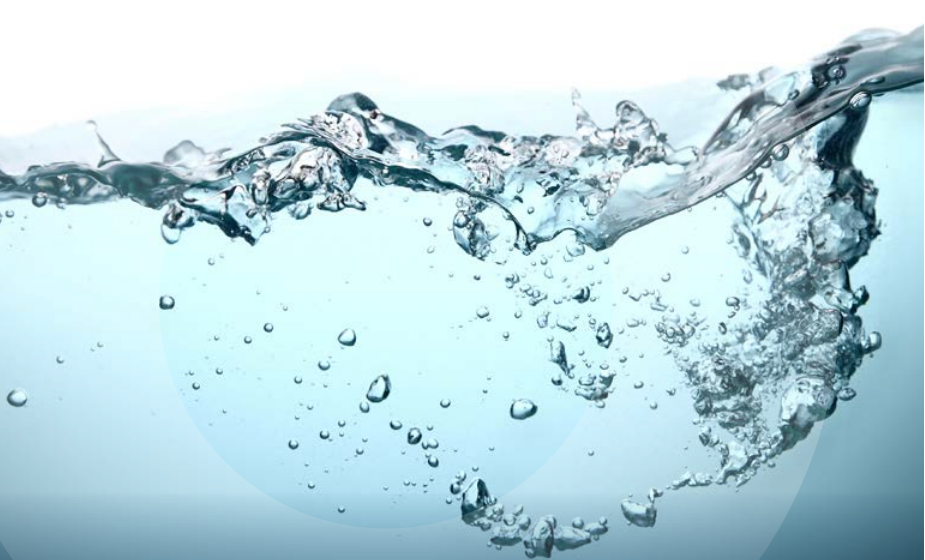
Read the full case story
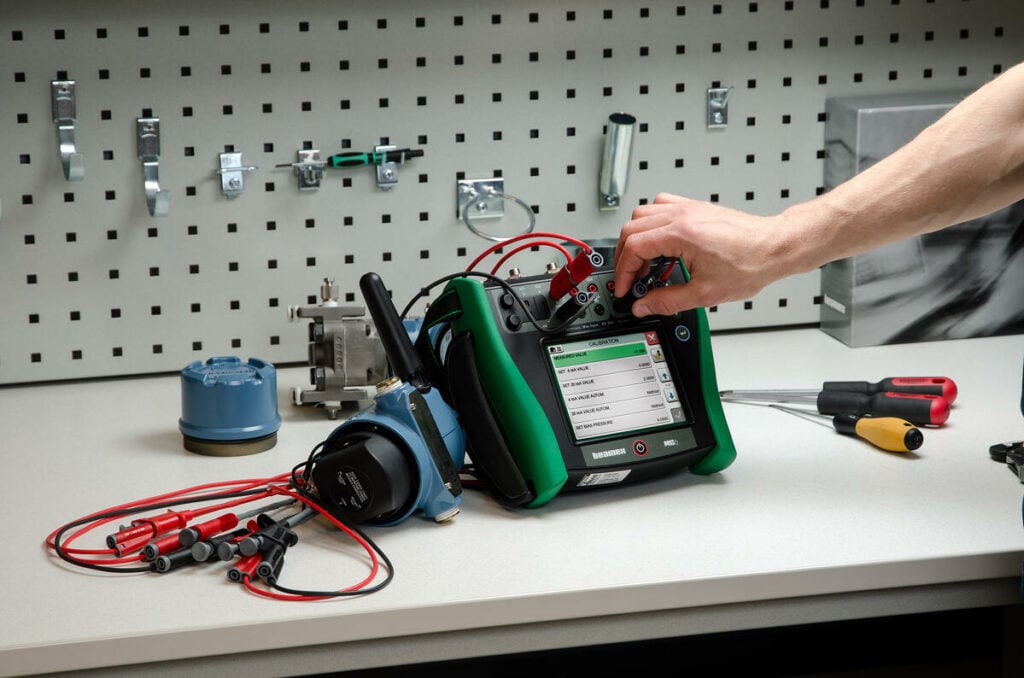
The plan comes together
Kevin has had extremely positive feedback from his team of technicians, who are unanimous in their opinion that the MC6 is far superior to their old calibrators. The utility’s operations staff can easily view and print calibration certificates, speeding up the process, and the regulatory agencies that the utility interfaces with have also reacted positively to the change.
Today, Kevin’s team of six instrumentation technicians manages over 1,600 instruments in CMX that need annual or biannual calibration. “This change has definitely helped to build trust between our utility and regulatory agencies,” says Kevin. “Adopting the Beamex calibration ecosystem and having Beamex as our partner for calibration excellence has helped us take a big step forward on our digital transformation journey. In my opinion, once you join the Beamex calibration ecosystem you never look back.”