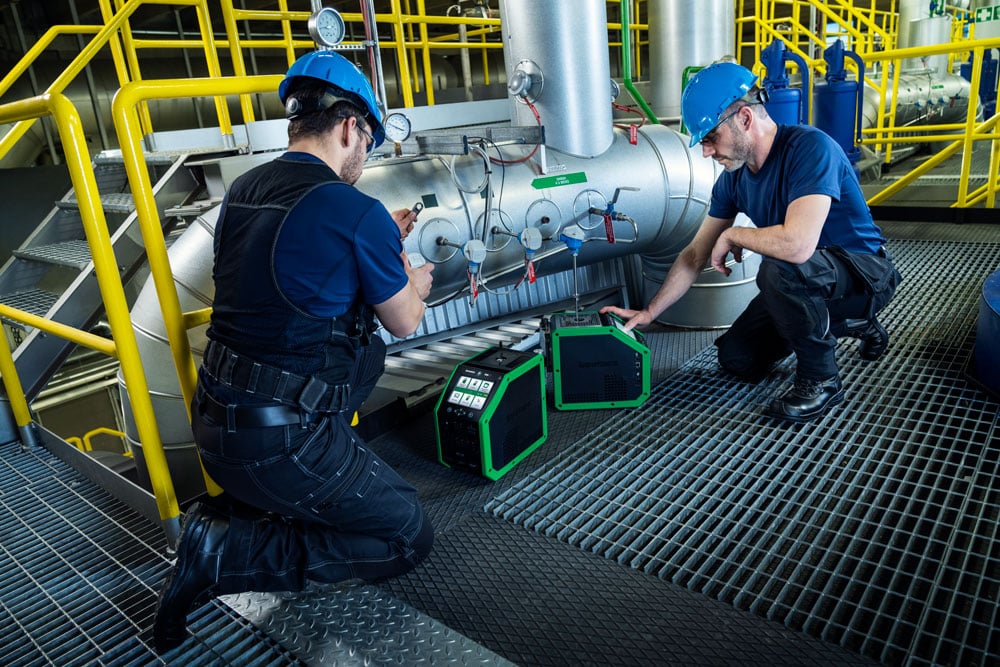
The rise of predictive technologies will need calibration
Jan-Henrik Svensson, CEO, Beamex
If you are reading this and are working for Tunturiverkko, kudos to you. Finland’s Northernmost utility, Tunturiverkko has the arduous task of ensuring regular power supply to Finnish Lapland. Installing and maintaining power in near Arctic conditions is a challenging task, with component failures being a common occurrence.
How did they solve this? By utilising the power of predictive technologies and an intelligent grid system that leveraged advanced sensors and machine learning. Tunturiverkko was able to predict three insulator failures in a single week, saving over 40,000 Euros.
Reading this example of predictive technologies in action in my home country, I could only marvel at its potential to dramatically ensure safety, security and efficiency in various industries around the globe.
The future of predictive technologies
A report from Emergen Research forecasts the predictive maintenance market to have a global market share of USD 70.05 billion by 2032. I think that number is likely to be breached as the use of AI increases and companies try to predict everything they possibly can.
So far, the capabilities of predictive technologies have been divided into three categories. Tech that is used for failure prediction, where data and machine learning predict direct and indirect failure of different components (As seen in the Tunturiverkko case). Then there is anomaly detection, which is a trend that I have seen showing strong growth in recent years. Here, predictive technologies are used to identify anomalies or deviances from usual operating patterns for equipment and processes. This can be both positive or negative and if identified and acted upon, can help businesses eliminate resource bottlenecks and unlock new opportunities. Finally, there is the use of predictive tech to calculate the remaining useful life of equipment. While these uses have already unlocked tremendous business value, it is but the tip of the iceberg.
Future uses of predictive technologies will become even more intricate thanks to a combination of AI, IoT and a bigger pool of connectable data than has ever been seen so far. Rather than only using historical data, I see predictive technologies using real-time data to fine-tune failure prediction, enabling companies to schedule maintenance years in advance.
Real-time monitoring will also help boost anomaly detection, allowing users to change strategies or tactics, and ensuring that their equipment is working at peak conditions all the time. I’d even go as far as to say that predictive technologies powered by real-time data will be an important factor in helping companies redesign their manufacturing lines and processes to take advantage of the latest market needs and trends. That would be the holy grail unleashing true predictive power.
What’s stopping predictive tech from scaling up?
The good news is that there are several successful pilots that one can read about to be convinced of the potential of predictive technologies. The bad news is that most companies are still stuck in the piloting phase and are working out ways to scale it up. What is holding them back? I see it being a result of technological disparity. At Beamex, we work with both calibration software and hardware and see the need to integrate IT and OT to get the full benefits of digitalisation. However, most companies are still in the early stages of their digitalisation journey and are struggling to integrate IT and OT.
They are stuck because they work with legacy technology, have old processes, or have safety and cybersecurity concerns. I meet representatives from many industries who don’t want their operations data to be connected to the cloud, they want it to be separate. While I understand their concerns, that thinking has to be changed if companies want to succeed in the increasingly competitive digitalised marketplace. When it comes to predictive technologies the saying “If it ain’t broke, don’t fix it” does not hold.
Trust and willpower will be the linchpins for embracing predictive technologies at scale.
Let’s start with trust. Here, data quality is critical. No amount of AI or futuristic sensors can provide accurate predictions when the underlying data is flawed. One must remember that a lot of historical data is still based on human input or at least human interaction. Then there is the quality of measurements (measurement error, environmental conditions, missing or corrupted data etc.) which must also be validated before it is included in the AI model.
I see calibration playing a critical role in maintaining data quality and security, providing the trust needed for companies to scale up their use of predictive technologies. Going ahead, rather than scheduling periodic calibration, I see AI-driven predictive tech using smart sensors and historical data to pinpoint when a measurement or data input might be off, triggering an immediate calibration event. Conversely, accurate calibration data will be used to train predictive tech to better spot these anomalies, leading to a win-win for all.
Of course, none of this is possible without willpower. Businesses just cannot afford to be intimidated by the prospect of leveraging predictive tech. You have seen how well your pilot projects have performed. You know the technology works. Now, you need to find the right people and create a shared vision to scale up these pilots. I believe that’s the only way for your businesses to stay competitive.
The convergence of predictive technologies and calibration will bring in a new era of industrial efficiency and reliability. As companies navigate the path towards digitalisation, embracing these technologies will shape a safer, more certain and transparent future.
You might also find interesting
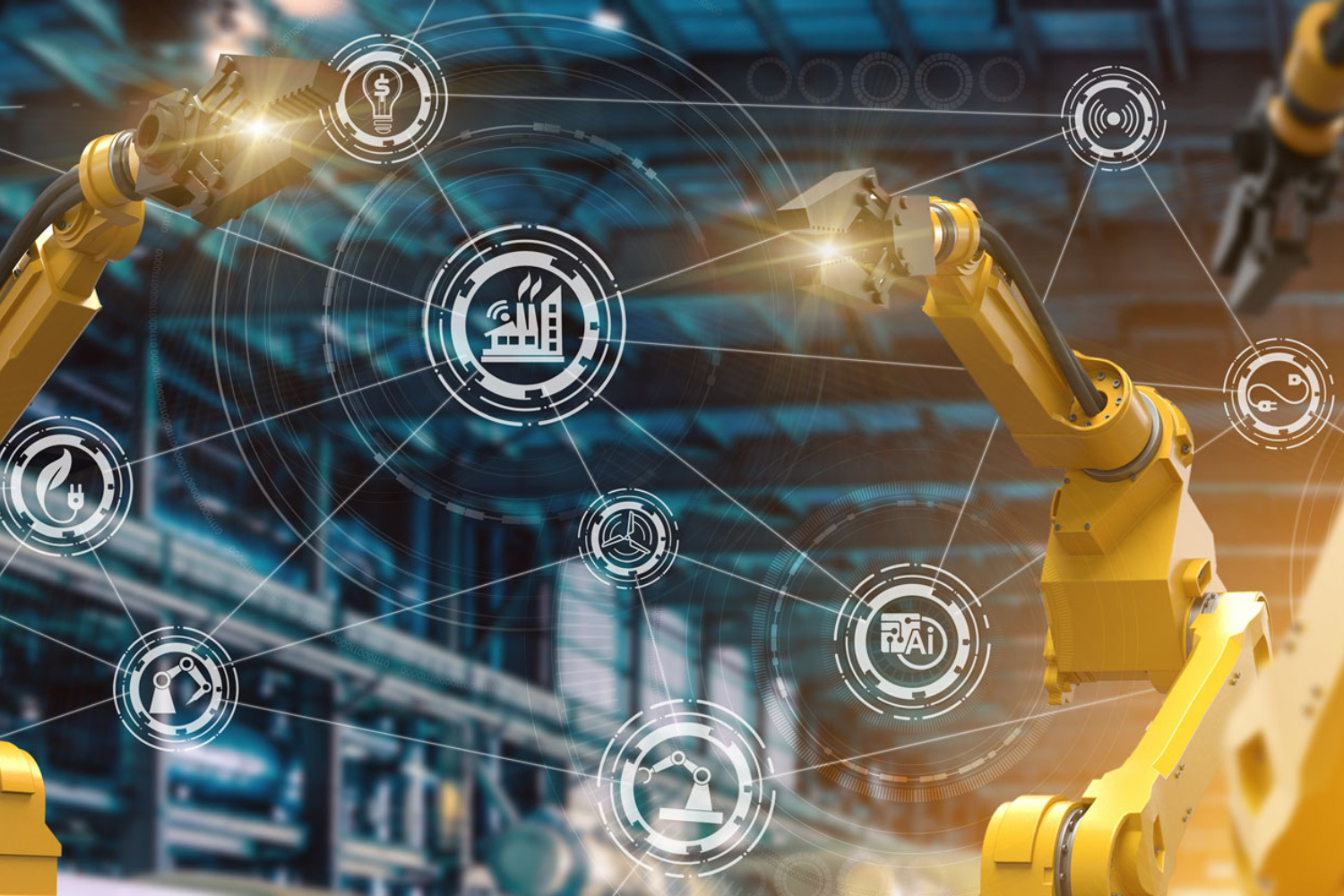
For a safer and less uncertain world
Welcome to our series of topical articles where we discuss the impact that accurate measurement and calibration has on the world and our everyday lives.