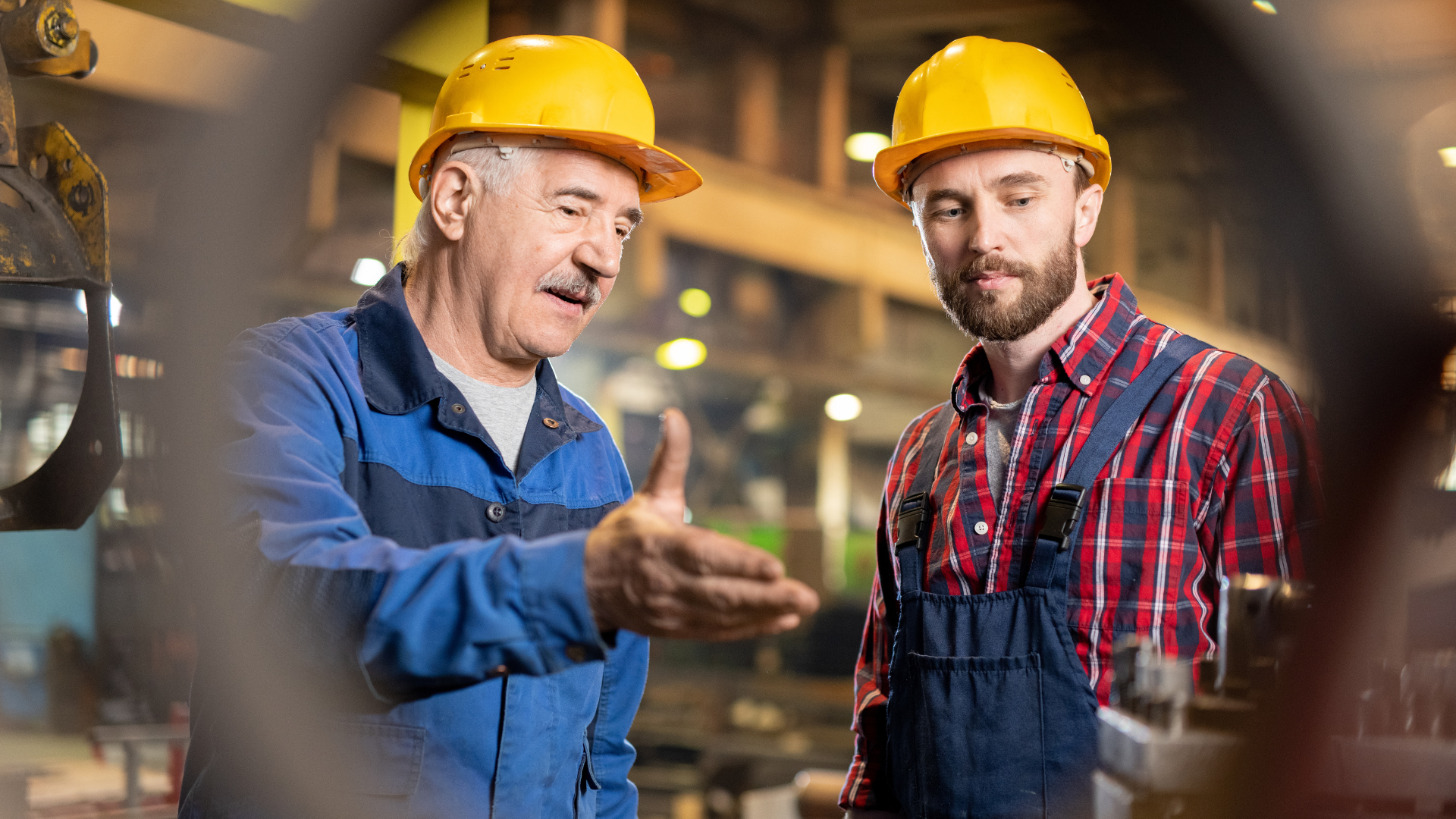
Capturing Silent Knowledge to Train the Next Generation of Workers
Sami Koskinen, Director of Digital Transformation, Beamex
Have you come across the following situation before? You are working in a factory where a high-pressure boiler is acting up. No one knows what is going on. The instruments don’t indicate anything is wrong. Then over walks this grizzled employee, who puts his hands on the boiler, feels its vibrations, and fixes it by turning a valve.
If you are in process industries like Oil & Gas, Chemical, Wood Processing, Manufacturing, etc, you’ve certainly met these experts. I call them the “macho men”. They are the ones you see handling wrenches, who know a good thump in the right place can get a machine working again. They know by the vibrations or noise equipment makes if something is amiss. They have developed advanced processes and solutions without being specially trained for them. They are the masters of their fields.
Their knowledge is not just technical skills. It is an understanding of nuanced processes, historical context, and problem-solving tactics honed over decades. With most process industries still adapting to digitalisation, as these experts retire, their knowledge is lost.
The big question then is, how do you pass on this “silent knowledge”?
Capturing silent knowledge
According to a survey by the Manpower Group of 40,077 employers in 41 countries, a whopping 75% of employers are having trouble filling open vacancies in 2024. That’s up from 36% a decade ago. Process industries such as materials, energy, utilities, automotive and logistics seem to be the most affected by this trend. The numbers match what I have seen in my interactions with leading players in these sectors.
Is there a way out of this? Here are my suggestions based on what I have seen first-hand working in calibration.
1) Use digitalisation for knowledge capture and management.
For many of these process industries, in Finland and in other countries too, there are no specific academic studies to train someone to work in these sectors. A case in point is the calibration industry. There are no courses you can take for such a niche and specialized sector. This can pose barriers for less trained workers entering the field. The solution then is to lower the bar. Digitalisation has a role to play here by facilitating the documentation of expert knowledge from seasoned workers.
At Beamex, we have developed technologies that work alongside human operators capturing measurements and digitalising them. This is then stored in our database along with other recordings that go back decades. This historical data can be then used to provide new employees with the expertise of everyone who has come before them.
Additionally, machine learning algorithms can also predict potential knowledge gaps and suggest training or documentation to improve this accumulated knowledge. These methods can be easily adopted by other industries.
2) Be prepared for the industrial metaverse.
The metaverse that a famous company tried to popularise may be dead. But I say long live the industrial metaverse. Technologies such as AR, VR and Digital twins are unlocking new avenues of growth with the industrial metaverse.
For example, AR and VR can create immersive training environments, allowing new employees to learn from virtual simulations of real-world scenarios. One idea that fascinates me is being able to digitalise the expert knowledge of the “macho men” while using AR/VR to create a digital copy or digital ghost. This digital copy knows all of the expert’s moves. Moves that have been optimised by years of work. Working alongside new employees, these copies share decades of accumulated knowledge and wisdom with a human touch.
Then there is the creation of digital twins of physical equipment that allow people to explore the mechanics of older models or variants ensuring that knowledge about the maintenance and operation of complex machinery doesn’t fade away. This is especially useful for process industries where legacy machinery and processes are the mainstay of operations.
3) Cultivate a culture of learning.
Technology is just one part of the solution, however. An organisation’s culture must support and encourage knowledge sharing. This involves establishing formal and informal mentorship programs where experienced workers can transfer their knowledge to younger employees. The use of technologies and digitalisation also makes it easier for veteran employees to record and transfer their knowledge.
Apprenticeship programmes are another solution, but not in the generic sense where it turns into a cost for the company. Instead, we make apprenticeship a mandatory part of one’s studies and covered by the government. This allows companies to train young students, making them professionals and taxpayers much faster, thus helping pay back the investment.
Finally, we must promote a culture of continuous learning where employees are encouraged to seek and share new knowledge regularly, and we recognise and reward them for their knowledge-preservation initiatives.
A strategic imperative
Silent knowledge is useful only when it is accurate, has been reliably recorded and can be securely shared. After all, we don’t want an inaccurate technique to be passed down to future employees. A key aspect to ensure this will be for companies to invest in secure methods of data sharing. It will require organisations to democratise access to data (As I wrote in a previous blog) to ensure the knowledge is effectively utilised.
Companies should consider the preservation of silent knowledge a strategic imperative. By leveraging technology and democratising access to data, companies can ensure that the invaluable expertise of their workforce continues to drive innovation and operational excellence for decades to come.
What other methods would you use to capture this silent knowledge? Get in touch if you have some ideas and let’s brainstorm new solutions
You might also find interesting
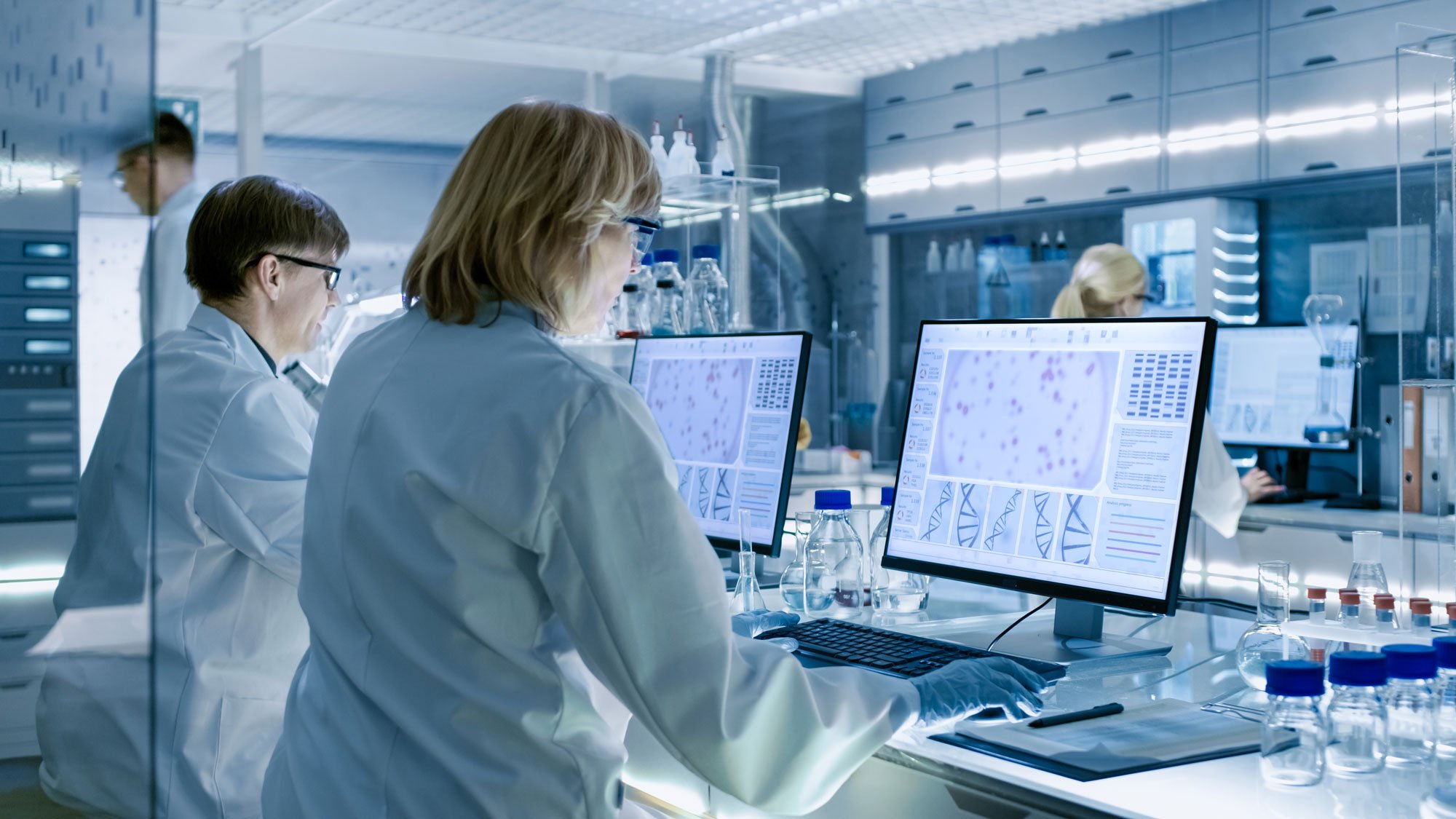
For a safer and less uncertain world
Welcome to our series of topical articles where we discuss the impact that accurate measurement and calibration has on the world and our everyday lives.