Summary
Through automated calibration, DC Water has been able to meet the increasing requirements associated with control system upgrades and evolving compliance. Implementing a paperless solution enabled the automation of manual work processes and these streamlined workflows enables them to accomplish more work with the same or less resources with a total return on their investment within the first year.
75%
Time saved on pressure calibrations
80%
Time saved on conducting calibration test procedures
100%
ROI in the first year
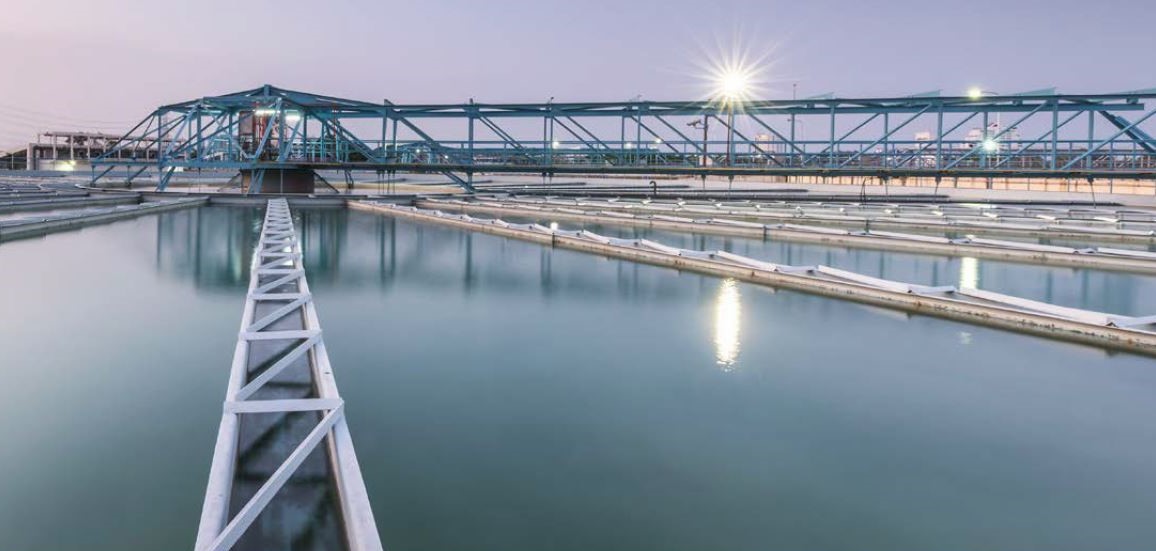
About the DC Water Blue Plains
DC Water’s Blue Plains Advanced Wastewater Treatment Plant opened in 1937. Currently it treats wastewater from the District of Columbia, Maryland and Virginia and is considered the largest treatment plant of its kind in the world. On an average day, close to 300 million gallons of raw sewage flows into the Blue Plains Advanced Wastewater Treatment Plant to be treated.
After treatment, the cleaned water flows into the Potomac River which leads to the Chesapeake Bay. To protect our waterways, DC Water is under strict requirements to dramatically reduce the amount of nitrogen and phosphorous in the cleaned water we discharge into the Potomac. In fact, these permit limits are some of the most stringent in the country.
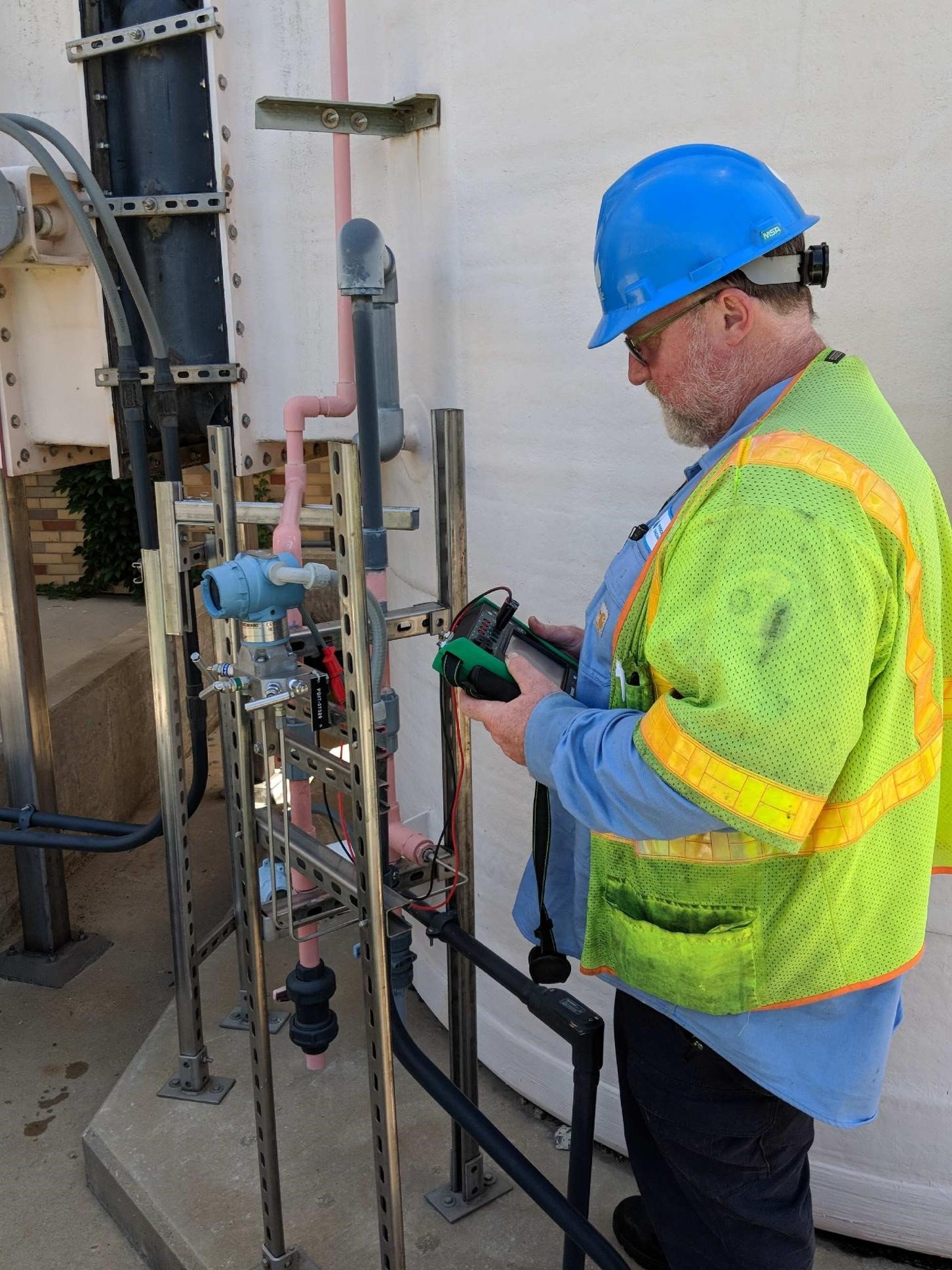
A better way with Beamex and process standardization
With the control system expansion and upgrades, there was a need for calibrating more instrumentation, competently calibrating smart transmitters with higher accuracy, and most importantly, better data for performance reporting was required by the Engineering Group.
The Maintenance Group needed to make substantial improvements to the calibration program to accomplish these objectives while keeping resources at current levels. A key component for success was automation. They invested in the Beamex integrated calibration solution comprised of Beamex CMX calibration software and Beamex MC6 advanced field calibrator and communicator, and pumps.
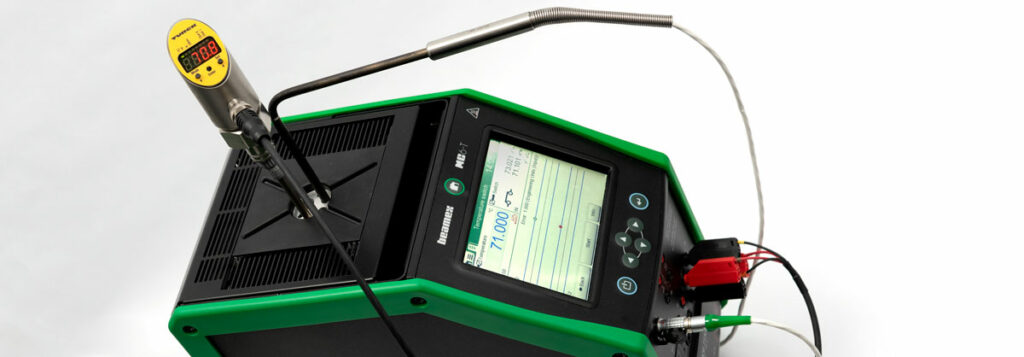
Documenting calibrations
A foundation to the solution was defining and documenting the calibration procedures for all calibratable assets into a database inside of the Beamex CMX software. These centralized and well-defined procedures could now drive methods that ensured measurement data is captured, measurement errors are calculated and compared to defined tolerances, and data is organized for easy access and reporting.
Building information assets provided the Engineering Group the information they needed for analysis, and the transparency and visibility greatly increased confidence levels for both upper management and third party stakeholders.
Achievements at DC Water
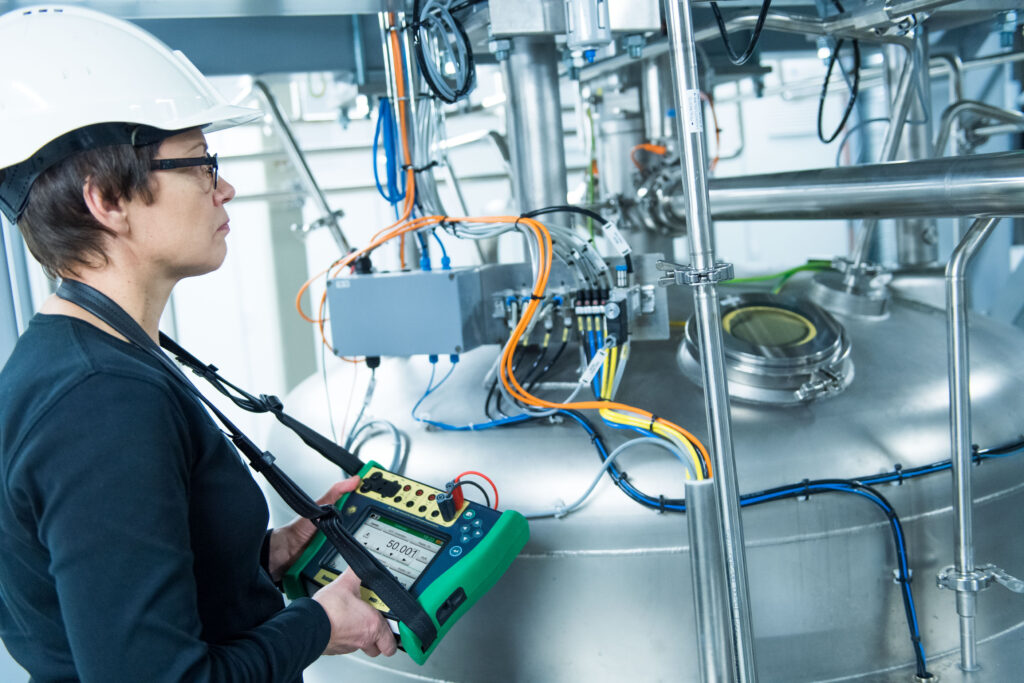
Better planning
Planning calibration work is now streamlined using CMX, yielding substantial time savings. The Maintenance Group uses fully electronic and paperless workflows by utilizing the MC6. Procedures are programmed into the MC6, measurement errors are calculated and presented in real time, and all measurement data is captured electronically.
Beamex MC6 >
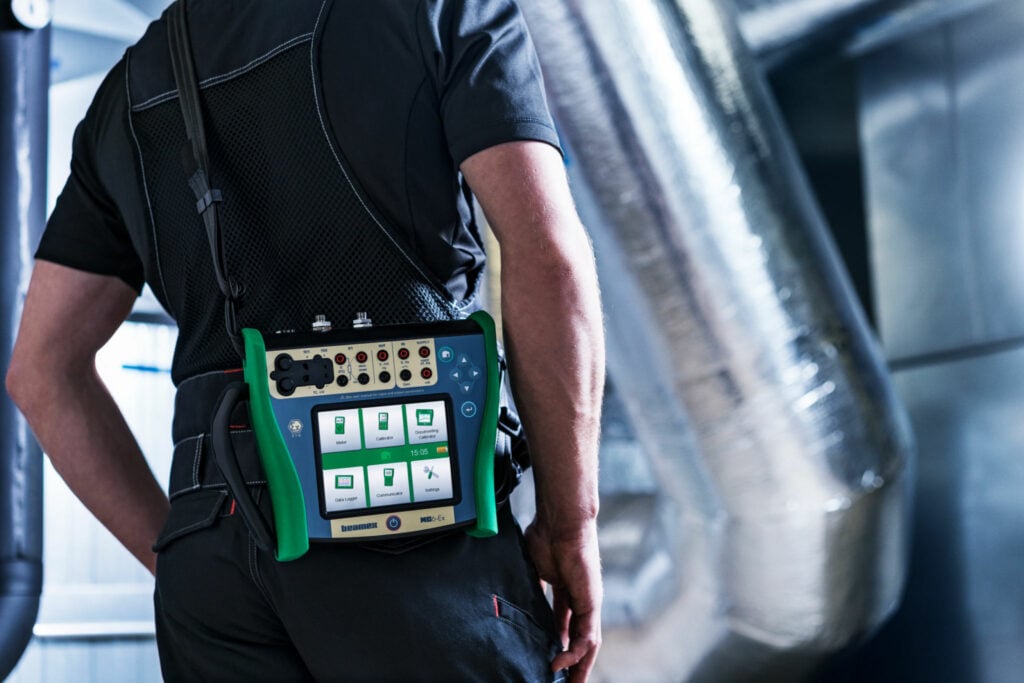
Quality improvements
In addition to time savings, there has also been substantial improvements to the quality of calibration. With the more streamlined workflow and automated documentation, they could now justify a more thorough strategy consisting of additional test points, as well as up and back down the span.
Beamex MC6-Ex >
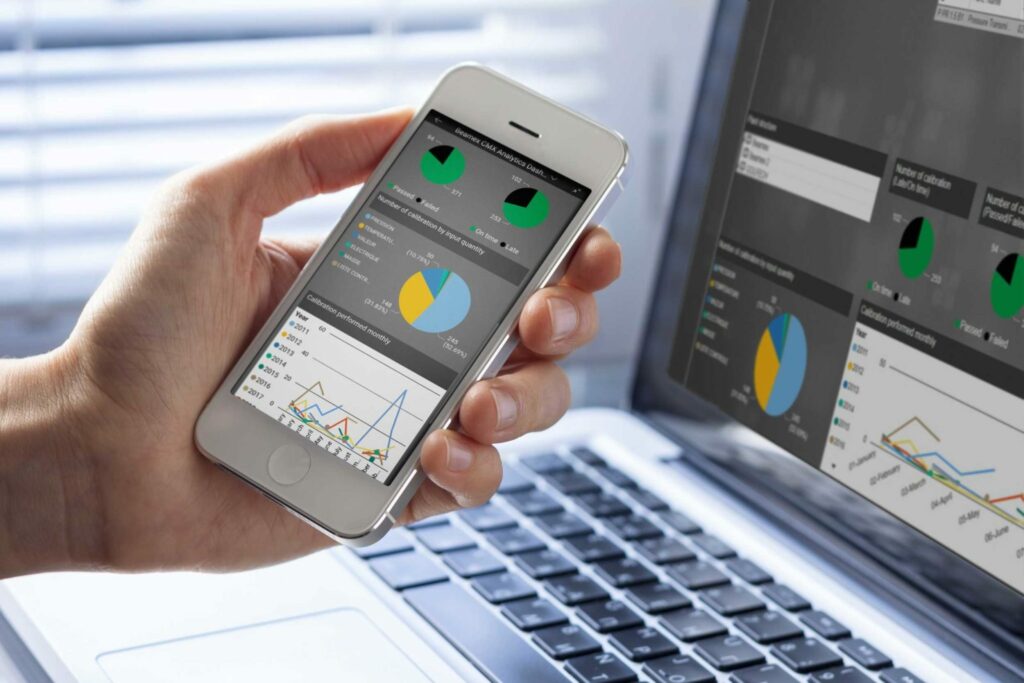
Documented results
With the CMX software, they have automated calibration. They can automatically generate calibration certificates and attach these certificates inside of their maintenance management system, Maximo. This provides transparency and visibility to management. The electronic documentation also minimized the opportunity for human error.
Beamex CMX Calibration Management Software >